제품 개발과 양산 과정에서 품질을 확보하기 위해 사용하는 APQP(Advanced Product Quality Planning) 방법을 적용한다.
하지만 이 과정은 여러 부서와 인력, 복잡한 공정이 얽혀 있어 다양한 리스크가 발생할 수밖에 없습니다.
APQP의 5단계를 기준으로, Product(제품), Process(공정), People(사람) 관점에서 발생할 수 있는 주요 리스크와 그에 대한 실질적인 대응 전략을 작성하였습니다.
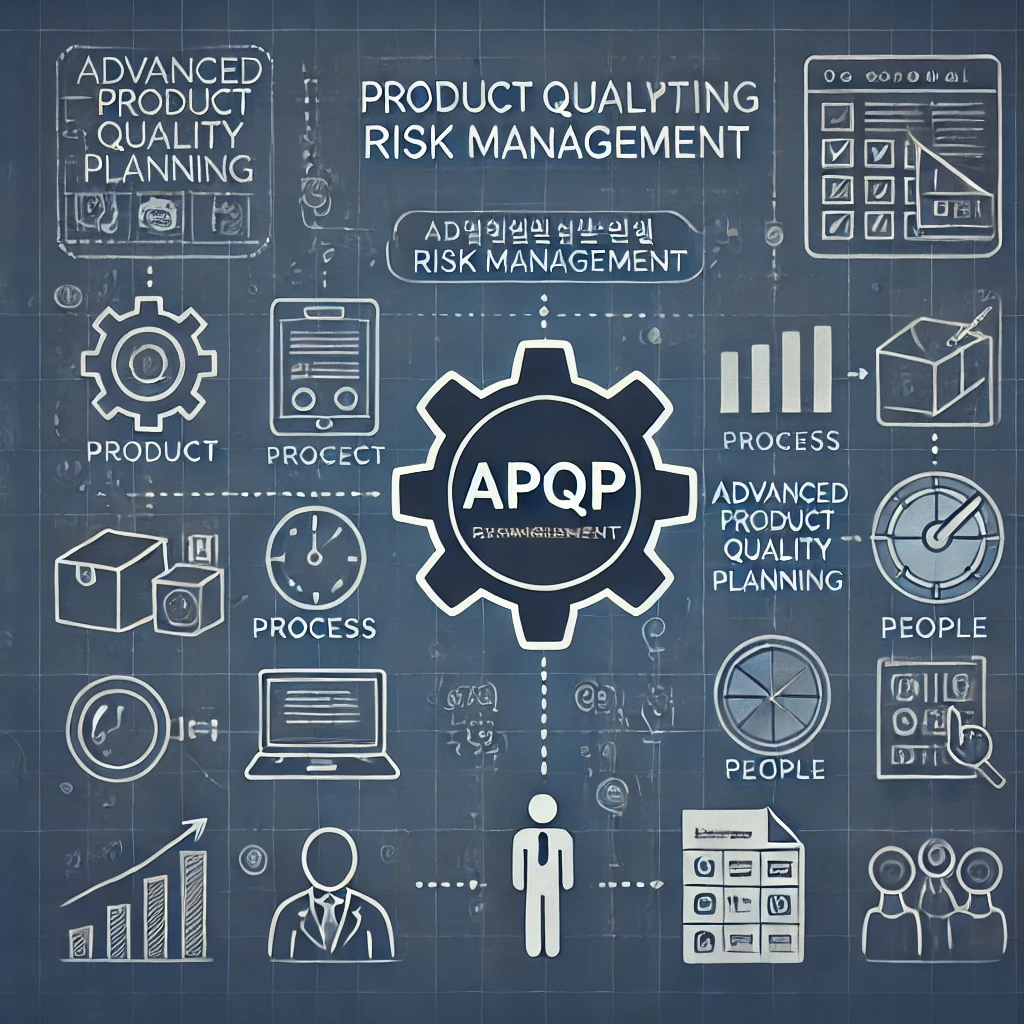
1 단계: 계획 및 정의 (Planning & Definition)
1) Product 리스크
- 고객 요구사항이 불명확해 설계 방향이 흔들릴 수 있음
- SOR(Statement of Requirements) 문서 작성 + 정기적인 고객 커뮤니케이션
2) Process 리스크
- 프로젝트 범위와 일정이 모호해 혼란과 일정 지연 발생
- 프로젝트 계획서 수립 및 공유 → 일정 관리 체계화
3) People 리스크
- 팀원 역할·책임 불분명으로 협업 저해
- 역할 정의 워크숍 및 정기 회의를 통한 협업 체계 구축
2 단계: 제품 설계 및 개발 (Product Design & Development)
1) Product 리스크
- 설계 오류, 고객 요구 미반영 → 일정 지연 & 비용 증가
- DFMEA(설계 FMEA) + 시뮬레이션 + 프로토타입 검증
2) Process 리스크
- 검증 절차 부족으로 결함 초기에 미검출
- 설계 검증 표준화 및 테스트 프로세스 강화
3) People 리스크
- 설계팀 기술 역량 부족
- 기술 교육, 외부 검토 도입, 협업 강화
3 단계: 공정 설계 및 개발 (Process Design & Development)
1) Product 리스크
- 원자재 품질, 공정 변수로 인한 품질 저하
- PFMEA(공정 FMEA)로 사전 리스크 분석 및 개선
2) Process 리스크
- 공정 불안정성 → 생산성 저하
- SPC(통계적 공정관리)로 변동성 제어
3) People 리스크
- 운영 인력 숙련도 부족으로 공정 오류 발생
- 교육훈련 강화 + 작업 환경 개선
4 단계: 제품 및 공정 검증 (Validation)
1) Product 리스크
- 제품이 품질 기준 또는 고객 요구를 충족하지 못할 수 있음
- PPAP(생산부품 승인절차)를 통한 철저한 품질 검증
2) Process 리스크
- 공정 검증 중 예기치 못한 변수 발생
- 초기 생산 시험(OTS)으로 사전 문제 파악
3) People 리스크
- 커뮤니케이션 부족으로 문제 해결 지연
- 정기적 검토 회의로 협업 및 대응력 향상
5 단계: 생산 및 지속 개선 (Production & Continuous Improvement)
1) Product 리스크
- 양산 중 품질 이슈 → 리콜 및 브랜드 신뢰도 하락
- Control Plan 수립 및 품질 실시간 모니터링
2) Process 리스크
- 공정 변동성 → 불량률 증가
- CQI(지속적 품질 개선) 활동 도입
3) People 리스크
- 피로도 누적, 숙련도 저하로 생산성 하락
- 교대 근무 최적화, 피드백 시스템, 작업 환경 개선
결론: APQP 리스크 관리는 ‘통합적 접근’이 핵심
단계별 리스크를 제품, 공정, 사람이라는 세 가지 관점으로 나누고,
이에 맞는 품질 관리 기법(FMEA, SPC, PPAP, CQI 등)을 도입하면
보다 체계적으로 리스크를 예방하고 품질을 확보할 수 있습니다.
리스크는 사후 대응보다 사전 식별과 예방이 핵심입니다.
철저한 APQP 관리는 곧 고객 만족과 비용 절감을 동시에 달성하는 열쇠가 됩니다.
Home : https://3rlab.kr
Mail : 3rlab@naver.com
Blog : https://blog.naver.com/3rlab
답글 남기기